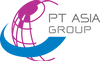
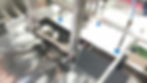
CASE STUDIES
Background
PEPSI-CO PepsiCo products are enjoyed by consumers more than one billion times a day in more than 200 countries and territories around the world. The beverage brands available in the Thai market are Pepsi Cola, Pepsi Max, Mirinda, 7-Up, Gatorade, Lipton Ice tea and Aquafina. In foods the company produces, distributes, and markets a variety of snacks under the brands of Lay’s, Lay’s Stax, Sunbites, Doritos, Cheetos, Twisties, and Tawan. In addition to snacks, the company has committed to continue providing more choices food and beverage made with wholesome ingredients that contribute to healthier eating and drinking, such as Quaker Oats.
PepsiCo Services Asia Limited is an affiliated company of PepsiCo Inc. and operates in the Foods & Beverages sector in Thailand. The company was founded in 1982 with the beverage business and expanded to the foods business in 1995, contributing to local job creation and providing technical support and market opportunity for Thai potato farmers.
Across the Kingdom, PepsiCo Thailand is supporting jobs, careers, and economic growth; fostering social well-being; and promoting environmental sustainability in ways that are advancing the government’s “Thailand 4.0” plan and National Strategy for economic development. Guiding PepsiCo is our vision to Be the Global Leader in Convenient Foods and Beverages by Winning with Purpose. "Winning with Purpose" reflects our ambition to win sustainably in the marketplace and embed purpose into all aspects of our business strategy and brands. For more information, visit www.pepsico.com.
Requirements
customer needs because the current production process uses human labor to load LD bags onto a beltconveyor, then the LD bags will run along the belt conveyor. The label applicator will apply the label onto LD bag. The manual feeding speed is 20 pieces per minute. The customer wants to increase production capacity to 35 - 40 pieces per minute and reduce human labor.
Challenge
It is well known that both large and thin LD bags It is very difficult to find a bag feeder or bag dispenser. Because the bag will have static electricity and if the bag is very thin the bag feeder or bag dispenser cannot be used using the Friction Feeder system. The only remaining method is to use the Vacuum Feeder system. But when using the Vacuum Feeder system, there are limitations to the feeding speed. This is the challenge of the PT Asia team.
Purpose
-
Reduce production costs
-
Increase labeling accuracy
-
Reduce the use of human labor in the production process
Selection and design of bag feeders
Pick and place feeder with conveyor is used to pick up the bags and place it for feeding.These machines are specially used for thin bags such as low micron pouches and papers with low GSM as most of the friction feeders are not suitable for such thin products, there are chances of getting torn so this pick and place feeder is specially made for such types of bags and papers
This Pick and Pace Feeder is workable for 40micron LD bags (Low desnsity polyethylene), The machine pick & place mechanism is pneumatically operated usng PLC based control panel, the timing & speed of feeding can be controlled, machine feature vacuum conveyor for thin bag so they travel without vibration & movement while printing or labeling applications, speed of feeding can be upto 35 - 37 cycle per minute and conveyor speed can be 20 - 40 meter per minute.
Design of a bag feeder or vacuum bag feed machine for large and very thin LD (Low desnsity polyethylene) bags. Many factors must be taken into account in order for the tool to work efficiently and reliably. Here are some important design guidelines and techniques:
-
Precise Vacuum Control: It is important to use a highly accurate vacuum system. To be able to handle very thin LD bags properly Proper control of the vacuum strength prevents bag destruction during the bag feeding process.
-
Suction head design: The machine's suction head should be designed to suit the size and thinness of the LD bag. A suction head with a wide surface area may be used to distribute suction power and reduce the risk of damaging the bag.
-
Sensors and Automation: Using sensors to detect the position and status of the LD bags allows the system to adapt and operate with precision. Good automation reduces errors and increases efficiency.
-
Durable Materials and Design: Because LD bags are very thin, the design of the bag feed should use durable materials and a design that reduces friction. To prevent damage to the bag during the process.
-
Dealing with moisture and static electricity: LD bags can be sensitive to moisture and static electricity. Design a system that can address these factors, such as using a static reduction system or controlling humidity in the work environment. It will help reduce problems caused by humidity and static electricity.
-
Easy Maintenance and Access: The bag feed design is easy to maintain and has easy access to all components. conveniently reduces downtime and increases machine reliability.
-
Testing and Adjustment: Before putting the bag feeder into production Thorough testing should be done to verify that all parts work correctly and efficiently. It is also important to customize it to suit the characteristics of the LD bags actually used.
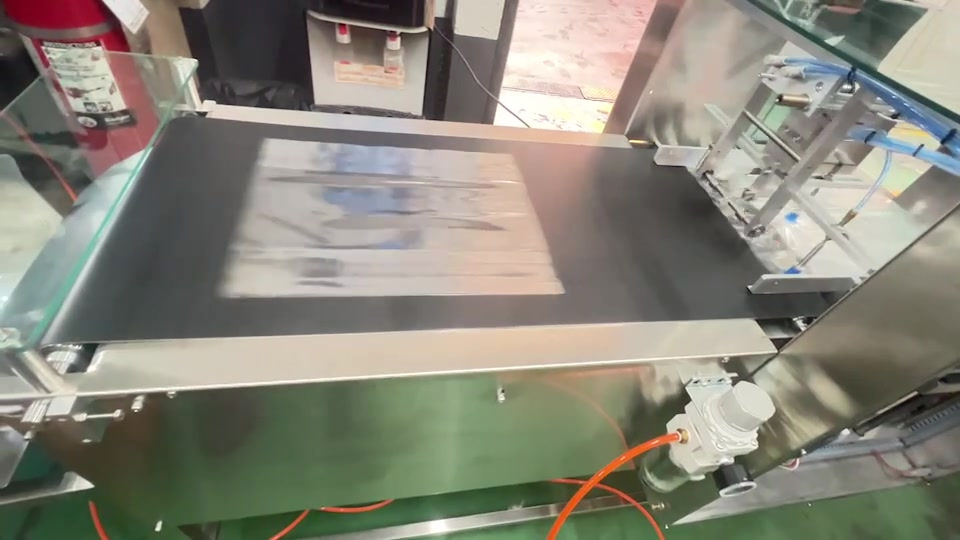
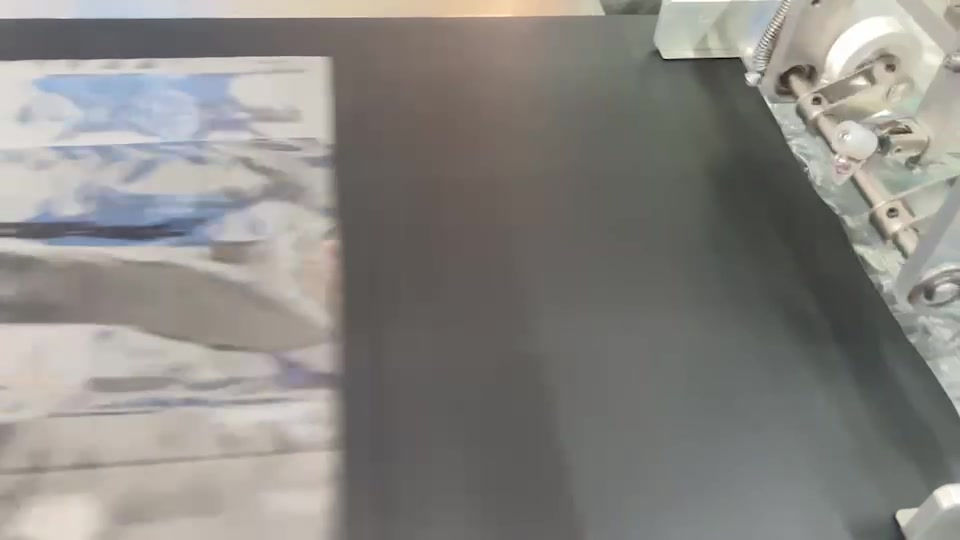