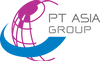
Energy drinking | 'Enercon' Induction Cap Sealing | 'TheSealCheck' Induction Sealing Integrity Verification System
Enercon Industries is the world-leading supplier of induction cap sealing technology across the globe. We have a sealer that is right for every production environment - from a low volume, start-up or testing facility, right through to the world's fastest production lines that currently run up to 100 meters per minute.
Induction cap sealing is suitable for various bottled drinks, including both liquid and powder products, whether chilled or ambient.
A strong, reliable, yet easy-to-peel seal ensures that the product is safe from spillage and contamination – reducing the risk of customer dissatisfaction and product wastage.
Another benefit that users of induction sealing cite is the ability to preserve the flavours and freshness of their beverages. By adding a foil seal oxidation is prevented, which helps keep the product fresh.
Induction sealing is also a suitable alternative for beverage manufacturers looking to move away from a tear band and become more eco-friendly. Adding an induction seal eliminates the need for a tear band and allows for the bottle’s neck and shoulder areas to be reduced – decreasing the overall closure weight and therefore the amount of plastic used.
The TheSealCheck is in end of line equipment in the primary packaging of beverage containers.
The TheSealCheck (Induction Sealing Integrity Verification System) is testing, in-line, the integrity of the aluminum foil sealing of induction-sealed bottles. Advanced Thermal Imaging Technology – a Paradigm ChangeThis first of its kind system, uses the most advanced. State of art, thermal imaging technology this groundbreaking technology, has the potential to cause an industry-wide paradigm change Renders the obsolete conventional inspection techniques that rely on destructive, imperfect, and often line-slowing sampling. Increased operational efficiency, reduction in batch failure.
Opportunity for more data-driven decisions. System CapabilitiesInspection through the closed cap thus enabling Induction Sealing Integrity Analysis without physical contact in an entirely passive, non–destructive fashion by performing. In-line inspection of each and every sealed bottle passing through the sealing line. Continuous process verification without slowing production. Ejecting defective bottles instantaneously upon being detected. The system is optimized for High-Speed Bottle lines of up to 250 bottles per minute. Most bottle and cap sizes and types can be inspected.
Any changeover from one size to another can be accomplished by simply choosing the corresponding bottle on the System’s touchscreen menu. The equipment is hardened for food and beverage production environments: All external system parts are fabricated from stainless steel or anodized aluminum, and the unit’s infrared camera is sealed against dust and moisture. The TheSealCheck uses cutting edge infrared imaging technology to inspect and reject induction sealed containers.