
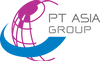

Induction Cap Sealing Liquid & Powder Products
Did you know that the type of product you are sealing is as important as other factors such as line speed and cap size? Dry solid products like popcorn kernels, tablets and capsules are the simplest to seal. However, liquids and powders require additional application considerations.
Sealing Liquid Products
When sealing liquids, the temperature of the product and the environment should be taken into consideration. A cold filled product usually requires more sealing energy than an ambient or hot fill product. This is because it takes more energy to heat the foil liner to the temperature required to melt the polymer and bond with your container.
Another consideration with sealing liquid products is if the product will come in contact with the liner and has any caustic properties such as with chemicals, or even tomato based products. In these cases a liner with a barrier layer will help protect the integrity of the seal.
Ideally the land area of the container should be free of any product residue prior to capping. If the product is flood filled or if there is a concern that there will be a liquid residue on the land area prior to capping, you should consult with Enercon’s application experts.
In many cases the residual product will be pressed off by the application torque of the cap, or it will evaporate during the sealing process. However products that may leave an oil type residue may undermine the sealing process and should be carefully reviewed.
Cap Sealing Powdered Products
Powders and granular products are excellent candidates for induction sealing. However, as with any sealing process, keeping the land area free from residue prior to capping is key for success.
Unlike a liquid product, powder residue may remain on the land area of the container despite the application torque of the capper, and the heat generated by the induction sealing process. This will cause failures in the induction sealing process as the powder or granule compromise the liner’s ability to interface with the container.
Solutions for this situation include following best practices for filling prior to capping, and may require the use of a device to either blow-off or sweep-off the granules prior to capping.
If the products are packaged in a hazardous environment, this indicates the presence of combustible dust in the air.
Examples of places with combustible dusts are grain elevators, flour mills, fireworks plants, spice, sugar and cocoa plants. Induction sealers should not be used in these environments and packagers should consult with Enercon for advice on how to integrate the benefits of induction sealing in special circumstances such as these.